Do you need a reliable, high quality brass welding service for your industrial machinery and equipment?
Do you need professionals who can work with complex brass alloys of different compositions and thicknesses?
Are you looking for a solution that will ensure the quality and integrity of your welded brass joints while allowing for fast turnaround times?
We present an efficient way of welding brass
We understand the importance of delivering high quality products on time.
Finding a reliable and experienced partner is a long-term process and takes a lot of time, but it is crucial for the success of your business, and a bad welder can have serious consequences for your business and jeopardize the quality of the product, which will be felt most by your clients/customers.
With two decades of experience, we have the knowledge and expertise to execute even the most complex projects within short deadlines, ensuring the highest standards of quality and brand recognition for our clients.
Brass welding is a complicated process that requires great knowledge, experience and quality equipment.
Our welding method, allows us to weld brass with ease, giving superior results.
Post-weld heat treatment is rarely necessary, but may be beneficial if the weldment is to be in highly corrosive conditions.
Due to residual stresses after welding, there is a risk of stress corrosion in service, known as seasonal cracking, in mildly corrosive environments such as ammonia or seawater. A welded object can be solved to a large extent by annealing at 260–300°C.
The alloys are resistant to corrosion and have excellent wear characteristics, so they are used for valves, bearings and machine parts.
As for history, the panels of the 1907 Rolls Royce Silver Ghost were made of nickel-silver, hence the name “Silver Ghost”.
With the exception of brasses containing lead (Pb), all brasses are weldable, and the lightest are low-zinc alloys.
The main problem in alloy welding is the porosity of the weld metal caused by the boiling of zinc during melting. Zinc melts at 420°C and boils at 910°C.
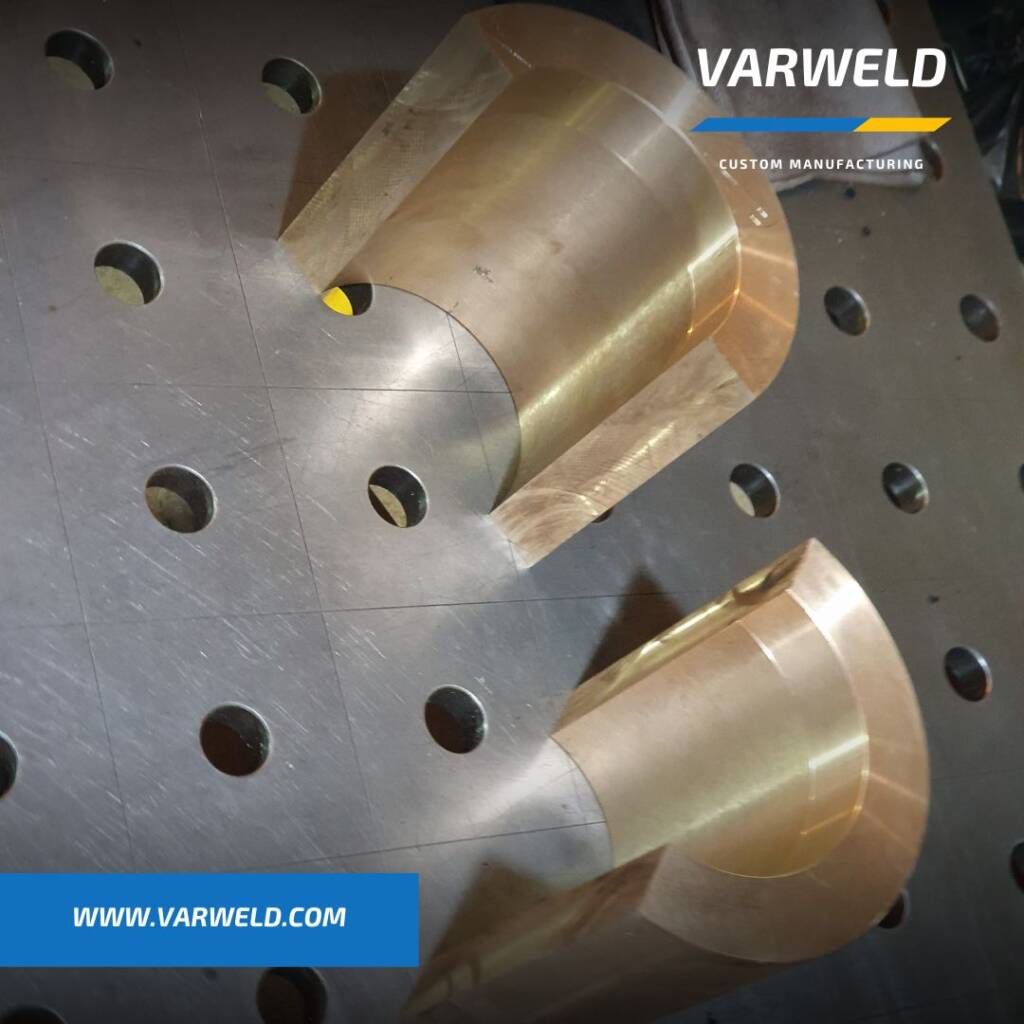
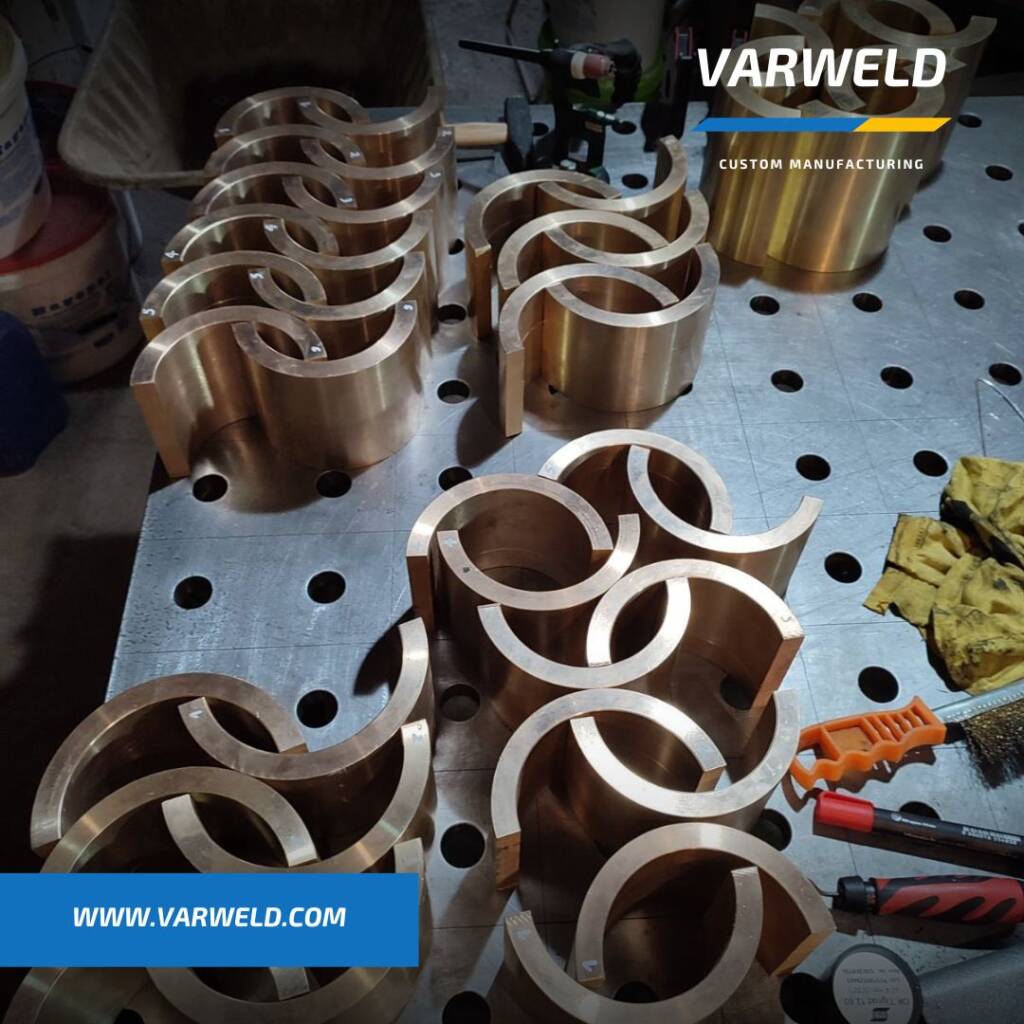
Boiling zinc can also lead to large amounts of zinc oxide in welding fumes and this can be a health and safety problem.
That’s why we only weld in well-ventilated rooms to prevent the release of dangerous gases during the process.
Brass is a difficult material to weld due to its high thermal conductivity, but our skills and expertise, along with our advanced equipment, makes the process easy and seamless.
Don’t take our word for it. our experience and satisfied partners and clients speak for us.
Contact us today to find out how we can benefit your project and improve the quality of your production. We will be happy to answer all your questions.