Precision and reliability are critical when it comes to fluid heat exchangers — components that often operate under high pressure, fluctuating temperatures, and in environments where failure is not an option.
Our CNC machining processes are designed to meet these exacting demands. From complex channel geometries to custom mounting flanges, every part is manufactured with tight tolerances and consistent repeatability. Whether it’s a prototype or serial production, our focus is on delivering components that perform with mechanical precision and thermal efficiency.
We work with a variety of materials including aluminum, stainless steel, and copper alloys, selected to meet the specific thermal conductivity, corrosion resistance, and strength requirements of each application.
Our CNC manufacturing capabilities for heat exchangers include:
- Milling and turning of precision components for both shell-and-tube and plate-type exchangers
- Machining of internal flow channels and complex geometries
- Drilling, threading, and surfacing operations to ensure exact fit and function
- Material selection and preparation based on thermal and mechanical performance needs
Each manufactured piece is part of a broader system — and we treat it that way. From the first cut to the final inspection, quality is embedded in every step.
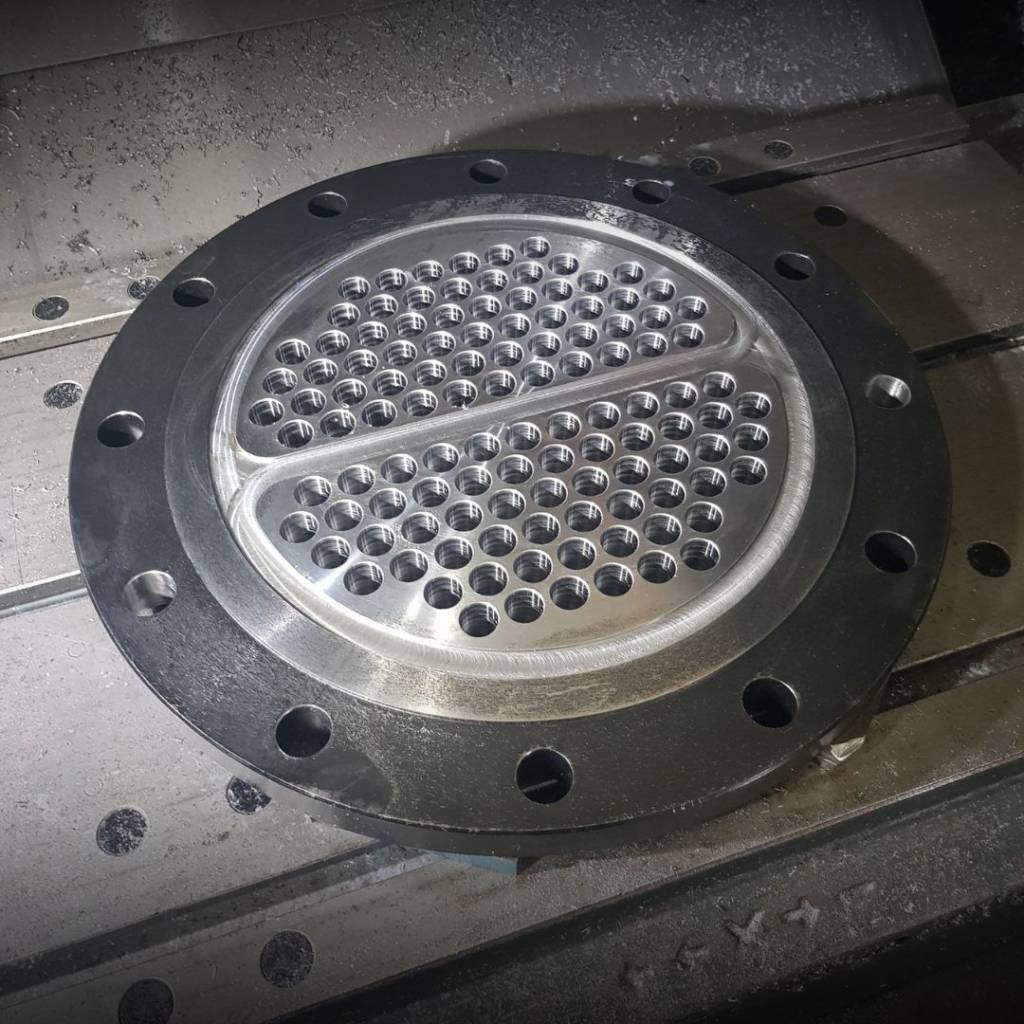
